Did you know that Clearaudio initially manufactured loudspeakers when it was founded in 1978? However, soon afterwards (from 1980) company founder Peter Suchy realized that his analog talents were much more profitable. And so my visit was dedicated to the Erlangen-based company’s now well-established cartridge production facility. And my first impressions in the production room very nearly matched my expectations.
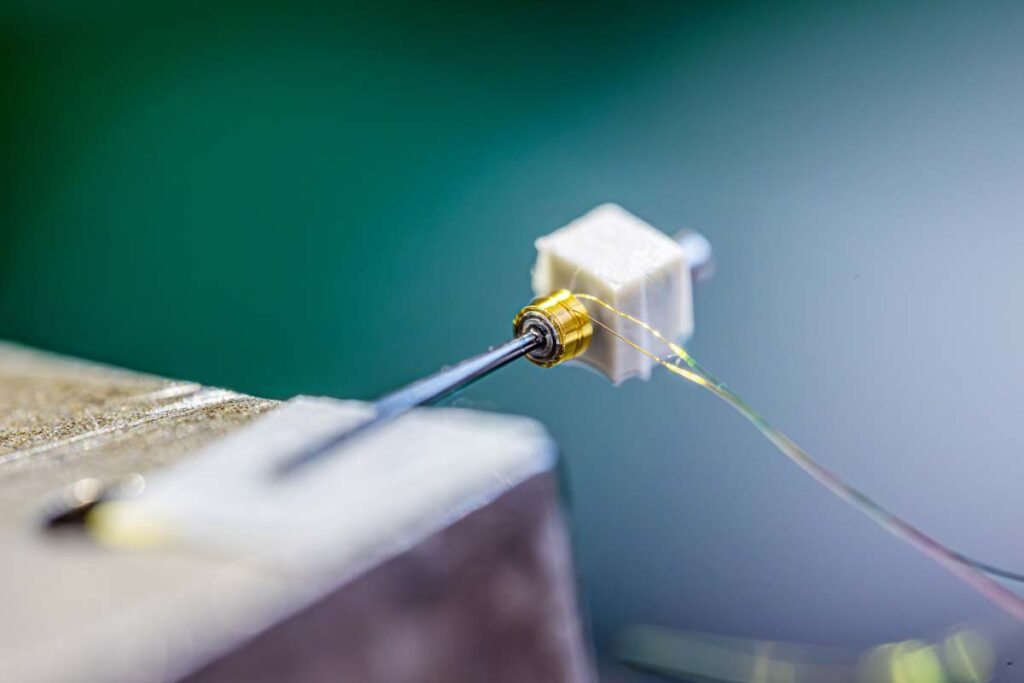
At several workstations, the pickup task force is working on a batch of higher-end MC cartridges. Ranging from the Talisman to models like the MC Jubilee and Da Vinci, and all the way to the Goldfinger, they are the pinnacle of the in-house portfolio. It’s a point of pride that these are made in-house by hand. Yet I would soon discover that the more affordable models are also made here at the very same stations. And many more, in fact, since, as is commonly known, Clearaudio doesn’t just produce its own 20-model lineup. The manufactory supplies OEM products to brands like McIntosh, Linn and other manufacturers. And then there are the various adaptations of existing designs for special lines, currently including the gold-gleaming MC pickups for an “Al Di Meola Signature” turntable.
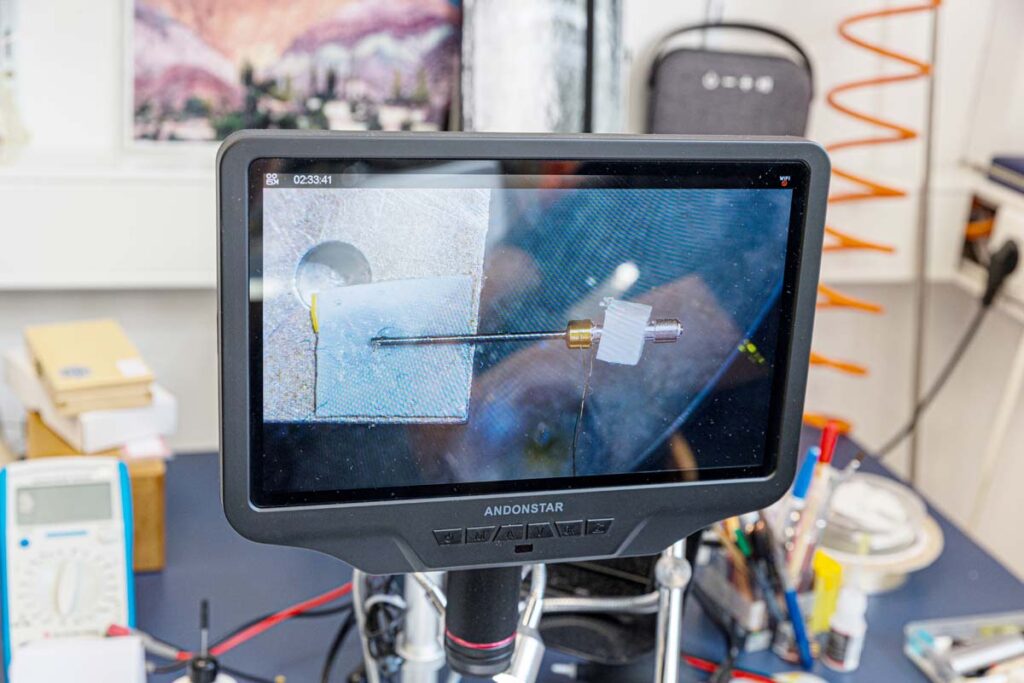
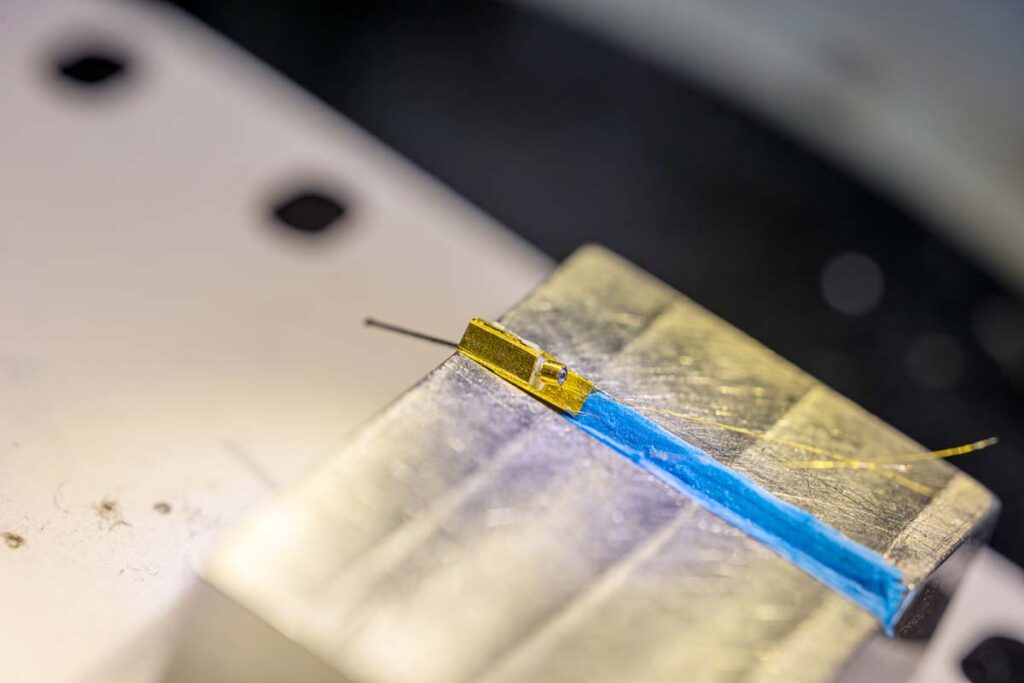
Lorena Machado explains why the production of smaller and larger models is strictly separated: The coils of the more affordable cartridges are made from copper, while those of premium pickups are wound with 24-karat gold. Dozens of OEM cartridges are being prepared for shipping in one part of the room, and she is sitting at a work table, looking at the monitor of a macro camera. Like most of her colleagues, she is a trained watchmaker. Working with these tiny components requires advanced sensitivity and experience, a keen eye, “and steady hands,” she adds, proceeding to outline the manufacturing process that is fundamentally the same for all MC cartridges:
All MC systems are based on boron cantilevers, into which a microscopically fine groove is milled before diamonds of different shapes are glued in, depending on the cartridge class. This is one of the few pre-manufactured components: these tiny needles could never be affixed by hand, so Clearaudio relies on a long-term supplier instead. Next, for further processing, the cantilever is glued into a jig. Lorena Machado threads a coil, then a tiny rubber damper, and finally another coil onto the cantilever. The protruding wires are barely a tenth of a millimeter thick, but still visible to the eye in the bright light of the workbench. Before assembly, the loose ends have been marked with Edding pens in the familiar red/white/blue/green scheme. These will later also be found on the cartridge’s terminals.
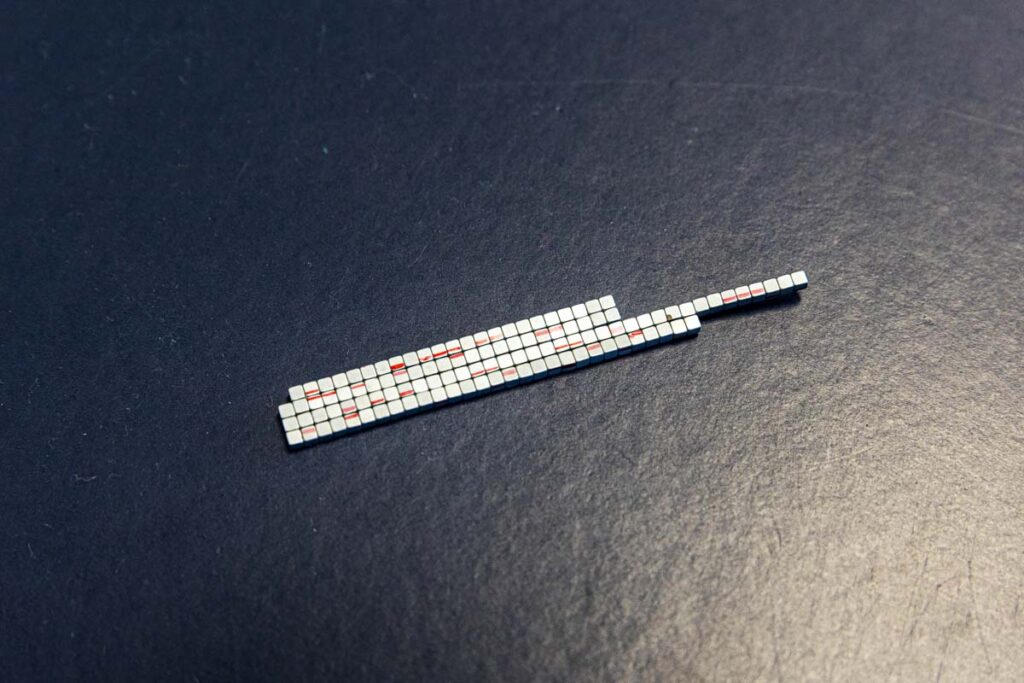
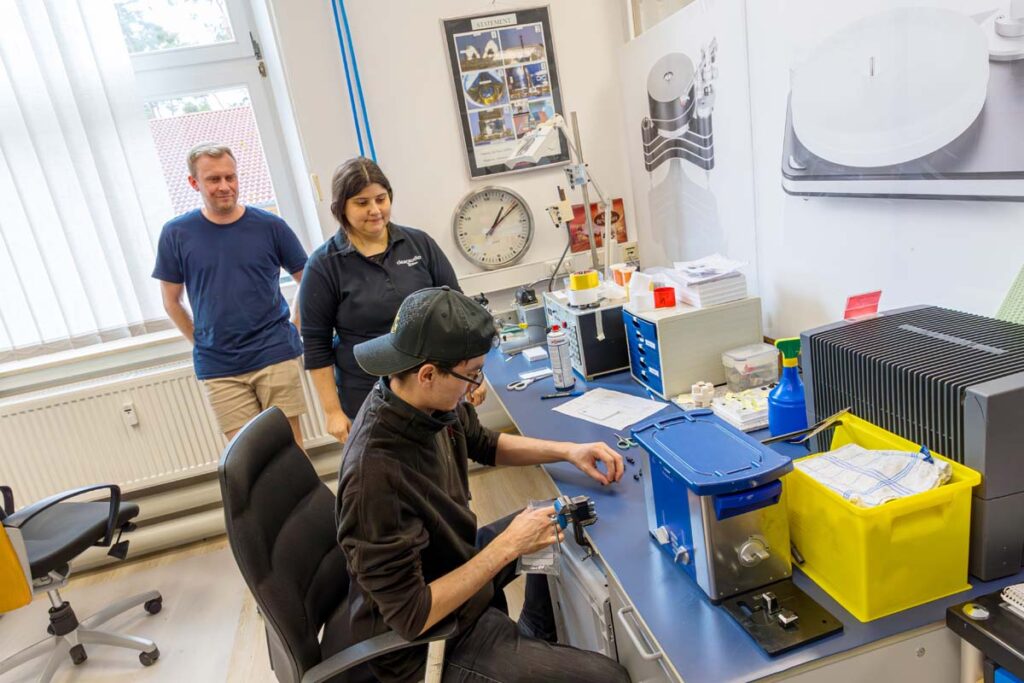
Stefan Kmuch, the company’s technical trainer, explains that the two coils represent the left and right audio channels. The damper in between serves both as both an insulator and a foundation for securing the cantilever in its housing. The number of windings is strictly defined, as it determines the cartridge’s impedance: exactly 50 ohms for the in-house MC models, which is approximately 140 turns for gold wire. Lorena Machado first inserts the finished cantilever into a small metal sleeve, and then into the tiny inner housing of the cartridge. Simultaneously, her colleague Markus Hempel is at another bench filing a dozen of the housings into shape. Hours earlier, he had cast them in another part of the building. This meant arranging eight miniscule magnets on either side of a comparably small copper ring before casting everything in a plastic compound.
As Lorena Machado explains, the cartridge’s quality level is determined at precisely the point when the cantilever is aligned in its magnetic housing. Even the slightest of deviations will lead to channel imbalances. And with a process this delicate, there’s no jig for assembly. Instead, it’s a matter of experience and a gentle touch. Naturally, the Clearaudio team doesn’t depend solely on that. Immediately after assembly, the watchmaker secures the raw pickup in a holder, connects the four wires to contacts, and moments later the needle is picking up its first signals at a measurement bench. Then, Machado adjusts the needle’s position with tweezers and measures again. At this point, they determine in which model the cantilever will ultimately end up. The selection process becomes increasingly stringent. In this case, we’re likely looking at a rather elevated Da Vinci.
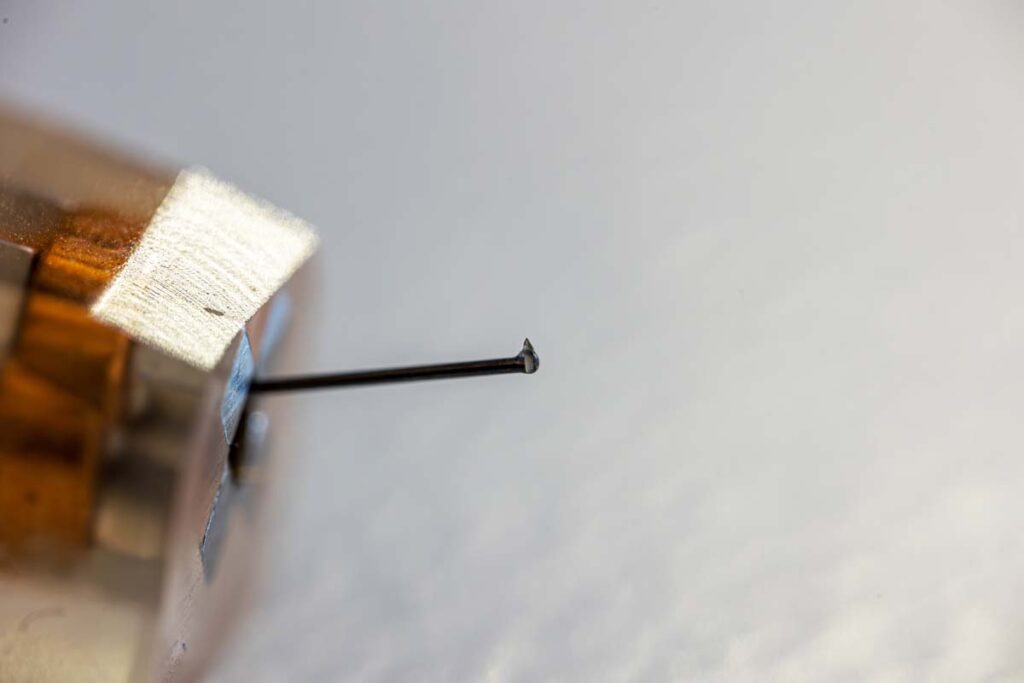
At this juncture, Stefan Kmuch interjects, noting that the measurement tolerances evidence the pickup’s precision, but for the system’s sound, they are just one of many factors. This is why Clearaudio manufactures so many different cartridges: the individual material mix plays a significant role. The outer housings made from plastic, wood, silver, or gold are supplied by different specialists. For the premium model Goldfinger, for example, Clearaudio commissions a goldsmith who casts, grinds and polishes each piece individually.
Before the handcrafted cartridge with its distinctive red housing is glued together, further corrections, fine-tuning and the final cleaning of adhesive residues are required. At this point I asked, how many cartridges could be made in this time-consuming process in one shift? And I received an answer that I could have guessed: On good days, it’s five to six MC models, and on bad days, it might be none at all. The entrance area has already filled up with boxes ready for shipping, and the three production employees reveal they have been at it for over a week.
During our conversation, I noticed countless printouts with photos hanging on the walls, showing cartridges, needles or other specifics. Stefan Kmuch explains that these are defective samples. Clearaudio is deeply committed to error analysis, and the images illustrate typical manufacturing problems, which make it easier for colleagues to recognize these issues. Further ahead in the room, there’s a whole catalog showing how a coil deforms when the cantilever directly above it has broken.
To conclude my visit, we briefly detour into the tonearm production area. Sales representative Niels Hoelscher leads me into a small room where three employees are busy with different production steps.
He indicates a detail that also applies to the cartridge production: Every model manufactured in-house has fixed workflows and a checklist that must be completed before packaging. However, the employees are free to sequence these workflows in any way that works best for them. Then, he shows me a prototype of the brand-new premium tonearm Unity, which already has “FIDELITY review sample” written all over it, so to speak. We’re scheduled to receive the sample in the coming weeks, along with a matching cartridge. We can’t wait.
Clearaudio electronic
Spardorfer Straße 150
91054 Erlangen
Phone +49 9131 40300100
info@clearaudio.de