How do you renew a traditional company without endangering old values? Piega has succeeded in this tricky balancing act. The brand was handed over to the next generation, creating space for innovative and fresh wind. But as soon as the new models start playing emotionally and powerfully, you know: the Swiss remain true to themselves!
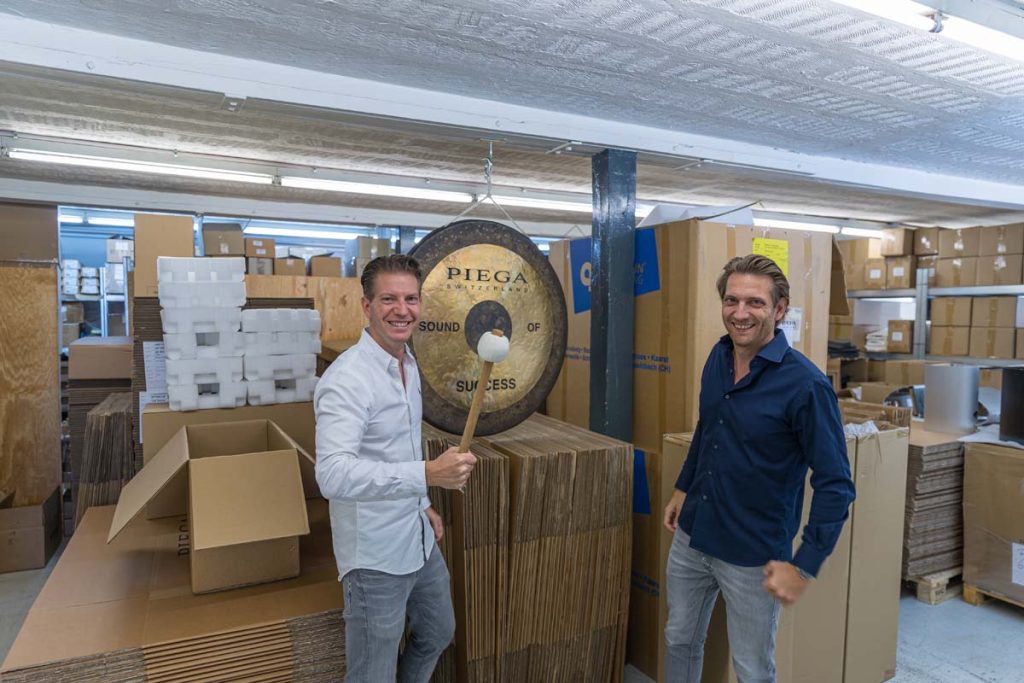
Horgen is a tranquil village on the western shore of Lake Zurich. It has everything that makes Switzerland Swiss for a tourist: a quaint village center on a gentle slope, traditional architecture, small stores, state-of-the-art infrastructure – and Piega. Anyone who knows just a little bit about Switzerland knows that the products of the loudspeaker manufacturer reflect many aspects of the Swiss Confederation. Exquisite ingredients such as resonance-calmed aluminum housings, high-tech adhesives or ribbon drivers meet as a matter of course with classic design approaches, loving craftsmanship and a team that has grown together. If you were also able to experience (I had the honor many years ago) how the cabinet strands are pulled in the aluminum factory under the pressure of several thousand tons, then you know that a hefty portion of natural force is slumbering in the speakers: “Next to the press, it feels like a loaded freight train is hitting”, developer Kurt Scheuch had promised us at the time – and was absolutely right.
But the purpose of my visit was not to describe the country and its people to you. Everything revolved around the profound change of the company: In the past years, Piega mastered a process that is currently causing headaches for many hi-fi manufacturers. The manufactory founded by Kurt Scheuch and Leo Greiner had to be transferred to the next generation. Of course, this requires more than just visiting a notary. In 1986, the founders were still among the “first front” of hi-fi innovators. While tinkerer Scheuch initially took care of the recognizable sound signature of the loudspeakers in a small garage and gradually discovered his interest in aluminum, Leo Greiner represented the company both internally and externally. The two did not have to analyze the concept of their manufactory to understand it, they designed it.
Greiner’s sons Alexander and Manuel, who today manage Piega in a commercial and sales capacity, faced greater challenges: They had to internalize the brand’s signature and “footprint”, find a potent replacement for Kurt Scheuch, and unite everything with their own ideas and visions in such a way that Piega still remained Piega in the end.
The manifesto of the successful transition stands physically in the listening room during my visit to Horgen: the brand new Master Line Source (MLS), the ultimate top model of the Swiss and so fresh that it has not even found its way onto the homepage yet. The name addition “MK-II” marks the generation leap and explains my initial irritation – in the run-up I had assumed an improved version of the next smaller MLS 2. Piega can be quite indifferent to the risk of confusion between the models. At the cost-adequacy of a single-family house in a decent location, the four-piece colossus is such an exclusive temptation that series production was not even planned. The “MLS MK-II LTD Edition” is a thoroughbred technology carrier, a flagship, and is to be custom-made in this capacity only a few times: “This unique speaker was made especially for you with love, care and attention to detail at Piega in Switzerland,” announces a bronze-colored plaque on the back of serial number 002, which I meet in the listening room. It is a pure stroke of luck that I experience it at all: the customer from England wanted to combine his new box with an experience and a trip to Zurich. He comes to hear them in Horgen before the black gems are carefully packed for their journey.
But first it’s my turn! Barely an hour after my arrival, development manager Roger Kessler thrusts an iPad into my hand. “I’d suggest you take this and have a good romp,” he says, and is gone shortly thereafter. Alone, I don’t feel. The two huge bass cabinets, only slightly lower than me at 178 centimeters, and two monolithic walls of ribbon tell me that everyone in the house will be there when I step on the gas right away. I lean back in my chair and kick things off with Fleetwood Mac’s “The Chain.” Guitar sounds ripple before the first hit on the bass drum jerks me back into an upright sitting position. Not what you’re thinking now: of course the kick sounds abysmal, authoritative and digs comfortably into the pit of your stomach via huge speakers with an efficiency of around 94 decibels. Turn up T+A’s HV electronics and the low end can get downright brute. What startles me, however, is the fact that I can perceive the drum in the room for a moment. From the center, a few centimeters to the right and barely two meters behind the speakers, a circular object flickers before my eyes with every pedal stroke of Mick Fleetwood – a shadowy image, in dimension and position so comprehensible that I suddenly get goose bumps. Probably the best image I’ve experienced so far – and the perfect prelude to an exclusive two hours with the MLS MK-II.
It continues with Led Zeppelin’s “Dazed And Confused”, which takes over the listening room with its atmosphere and coolness. The voice of Robert Plant announces tangibly and vividly the qualities of the newly developed coax ribbon. The multi-part nature of the MLS ensures perfect localization of sound events: The Piega team sought out the spots in the room for the bass cabinets, each weighing 200 kilograms, where they would work perfectly, and then aligned the slim midrange/tweeter units (no less heavy, though, at 100 kilograms each). As a conglomerate of four perfectly balanced line arrays, the MLS MK-II radiates sound in the form of line waves. Several times I bend over, duck in my chair, some times even stand up completely. No matter in which vertical position I hold my head, the total of 30 drivers remain “in phase” and sound identical in every sitting position without a trace of interference. The quite large Piega listening room is at the lower limit of what is possible, as I later learn. A loudspeaker of this size and performance class requires a lot of room to breathe.
My listening tour leads me on to Kraftwerk’s “Radioactivity,” a Beethoven Allegretto, Holst’s “Mars,” and finally to the wonderfully woody organ of Philip Glass’ “Prophecies” – at this point I’m no longer alone, as marketing manager Roman Walser has joined me and is listening in curiously. Afterwards I feel like more “solid” material, I listen to an intermezzo of Ambient-Electro (Boards of Canada, Aphex Twin, Louisahhh) and finally work my way up to some Alternative Rock by Rage Against the Machine and then on to some snappy Pop Ă la Eagle-Eye Cherry. The MLS plays along confidently, because as a sophisticated all-rounder it can handle everything on a comparably high level. The only limits are the quality of some recordings.
After tearing myself away from the MLS, I take a tour of the house. Employee Mario Ballabio explains to me all the steps that he, his colleague Jasmine Keller and daughter Ailina Ballabio, who works at Piega while studying, have to take into account. I have already been able to follow his explanations on several occasions, but I am always surprised anew at the precision with which the three of them go about their work: The supplied wafer-thin capton foils are processed with concentration, a sense of proportion and a thousand times rehearsed hand movements. I witness Jasmine Keller gluing elongated damping strips to the back of tweeters, which – once near the ribbon – find their way to the foil as if by themselves. This has to be right the first time. She then uses a scalpel to make four small incisions on the edge of the tweeter, giving them more freedom of movement and bandwidth. “For that reason alone, we’ll never be a big mass producer,” Ballabio explains. There is a physical upper limit to the number of ribbons that can be produced each day, he says. This is especially true, he says, for the complex coaxial midrange-tweeters.
On this occasion, I learn a detail that had completely escaped me until now: in fact, the Swiss do not manufacture a state-of-the-art coaxial ribbon (as I always thought), but rather an adapted version for practically every loudspeaker model. The widths of the counter-phase wired traces, magnets, size and freedom of movement of the tweeter (correctly: the cuts) are adapted to the variables of the particular model and its cabinet. Actually logical: the coaxial drivers must match the number and efficiency of the bass drivers used. On shelves I discover a good dozen mounting frames for different variants and generations of the complex ribbons. The types are consistently numbered. Ballabio points to a frame with the 211 and tells me that I just heard them in the new MLS MK-II.
A little later, I’m sitting in the listening room with development manager Roger Kessler, reflecting on the experience. He is one of the “newcomers” to the company. Previously, he worked as an audio engineer in the automotive industry, integrating car hi-fi systems for BMW. The fact that different approaches apply in such an environment is evident from the answer to my first question: I tell him that I think it’s a huge challenge to improve a loudspeaker like the Ur-MLS in the first place. Where do you start? Analysis and troubleshooting, Kessler replies, adding that you can actually always find something to refine. The MLS MK-II was developed as a joint effort between the old and new guard. Kurt Scheuch developed it together with Daniel Raymann. He himself had brought to the company above all his knowledge of measurement technology, analysis and computer-aided simulations. Only this made Piega capable of realizing a product like the Ace Wireless. Since their active modules are manufactured in the Far East, trial and error was virtually impossible. So Roger Kessler and his team simulated all the parameters of the three models in the computer and tuned the boxes in a “binary” way. Only when all the individual components had been delivered did it become apparent that the calculations were correct. The wireless speakers are therefore not only a new product in the Swiss company’s portfolio – their development history is also unique.
With the MLS, on the other hand, the development team had looked at countless parameters of the enclosures and drivers on the measuring table and discovered a number of small, sometimes tiny points of attack. However, underlying problems of the previous designs were not brought to light: “The times when you screw on an adjusting wheel and achieve unbelievable changes are over,” he explains to me. But the many details also resulted in a noticeable step forward.
Thus, the UHQD Graphene woofers from SEAS were better integrated with the housing concept. The change in weight by coating the diaphragms was enough to optimize the behavior of the 12 drivers. In addition, Kessler replaced the previously separate midrange and tweeter ribbons with an identical number of coax ribbons. For more control, the nearly massless drivers are covered with a foil on the back. Meanwhile, their enormous bandwidth remains intact: The new “211s” also play up to 50 kilohertz. Kessler then retuned the crossovers. With 24 decibels per octave, they are quite drastic, but in a Line Source, despite a total of 30 drivers, only two crossover frequencies are required at 460 and 2800 hertz. The final tuning was the biggest challenge with the MLS MK-II. After all, the microphone of the measurement software does not know that it is a line source. And so – as always – the constant listening, checking and enjoyable music listening still remains the decisive step …
PIEGA SA
Bahnhofstrasse 29
8810 Horgen
Schweiz
Telefon +41 44 725 90 42
mail@piega.ch