Rene Wiedner is an organizational sociologist at Warwick Business School, which is part of Warwick University in Coventry, England. He studies change processes in organizations and industries and the relations between work and technology. He began looking into developments in vinyl record manufacturing about 8 years ago.
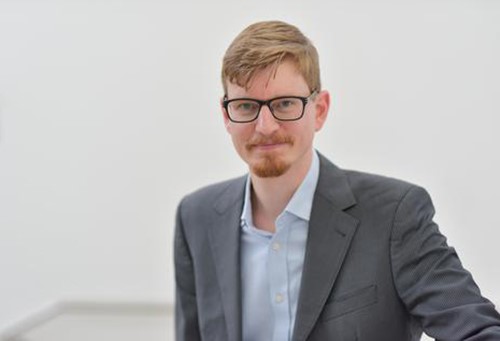
The Business of Why Vinyl Has Survived was originally published in Copper Magazine issue 209
FIDELITY cooperation with Copper Magazine
Read this article also on Copper
As Rene notes, “what intrigued me was how a technology that essentially had been written off several decades earlier had been kept alive. I wasn’t interested in the vinyl revival and understanding why sales of vinyl records have increased again. I was interested in understanding how makers of vinyl records had kept going.”
To gain insight, I had a conversation with Rene.
Frank Doris: How did you get involved with studying vinyl record manufacturing?
Rene Wiedner: I had just finished my PhD at Cambridge University in 2015. I had always been interested in music and anything related. A good friend of mine is a recording engineer, living in London at the time. He was telling me interesting stories about what was going on in the world of vinyl. Around this time there was already talk about a vinyl revival, but I wasn’t that interested in the revival per se. I was interested in some of his anecdotes about how there were issues with lacquer mastering discs and so forth.
I thought it’d be really interesting actually to study how this industry or this technology – I didn’t even know what I was looking at exactly at this point – was kept alive in the digital era. I kept studying it for many, many years and it became more and more interesting over time.
So you’re studying the vinyl industry more from a, I don’t know if sociological is the right term for your viewpoint…
Yes. More from a sociological rather than a strictly economic or technological point of view.
It seems like vinyl manufacturing has entered an entirely different paradigm from back in the day when the compact disc was supposedly going to kill it forever. Then, you had big companies and big pressing plants, and you’ve told me previously that now it’s the opposite, with the industry shifting from large corporations to smaller vinyl-making operations. How did that happen?
There has been a major transition and it is down to quite a few different factors. Back then, the big record labels owned their own pressing facilities and would actually make the physical products. In the 1980s and the 1990s, these companies were trying to outsource as much of that as possible and become purely marketing companies, This coincided with the advent of digital audio, where they were like, “well, why should we invest in all of these digital capabilities? Why don’t we just outsource that to other companies?” So, the big companies just kind of exited production in general, not just vinyl record making, but production in general.
And it wasn’t just the music industry. This was happening in other industries as well. This was a time when companies were being told to just focus on one thing and do it well, and if they didn’t have to do it, outsource it. But there were a few small vinyl manufacturing companies even back then, and they’re the ones that actually kept going. They didn’t have the pressure to sell that off. You had some family businesses in the US but also across Europe, and in Japan that were either making records or somehow involved in the industry.
Some of those kept going because they never had to make huge volumes of records to stay alive. They could focus on a niche market. And I guess they had loyal customers, especially if they were located in a particular region where vinyl records were still valued. So, Detroit for instance, there was still some demand there, and in Germany and so forth, especially for electronic dance music.
But then what I found to be really interesting was that people actually entered vinyl record manufacturing when it really looked like it was going to completely die out. They took on the risk. To see somebody do that in an industry that everybody says is basically dead, basically people would think you’re completely crazy, right?
That’s the audio industry. That’s us!
Certainly, audiophiles kept the whole idea vinyl alive. I remember going to my first CES in 1988 for The Absolute Sound, and we were getting hammered by the mainstream audio press, who thought digital was “perfect sound forever.” I went around the show with Michael Fremer and couldn’t believe the amount of undisguised hostility towards us. But audiophiles and DJs kept the vinyl flame alive.
You mentioned that innovations in vinyl making were happening around this time. I would have thought exactly the opposite.
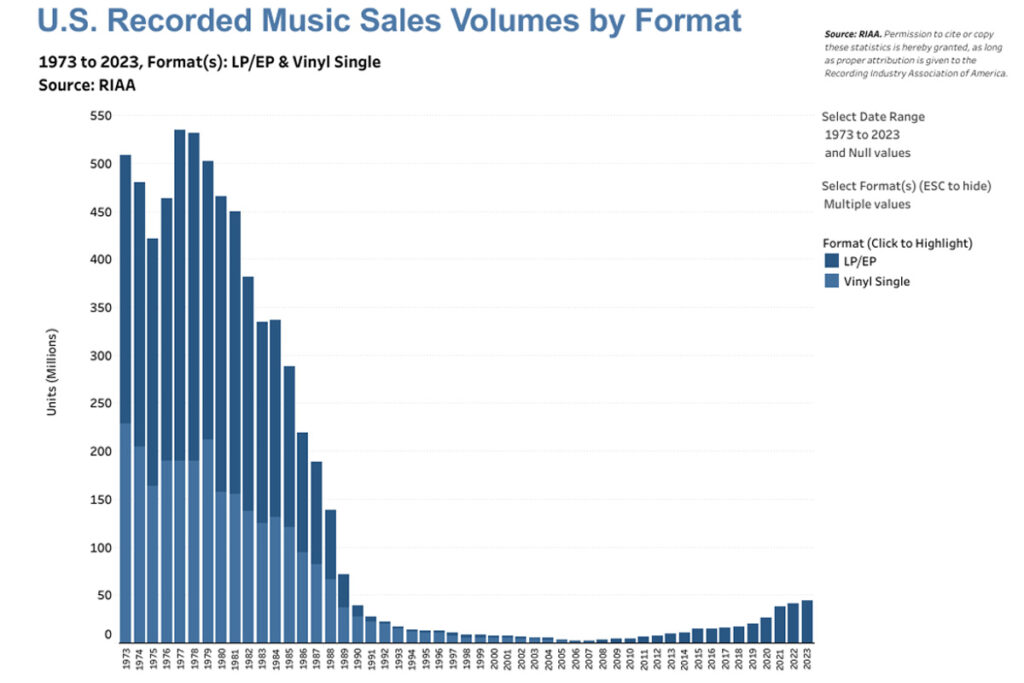
Obviously most companies were trying to innovate in the digital domain, but other people were trying to repurpose vinyl records in some way. It was no longer for mass consumption anymore. It became more of a niche. That necessitated a different way of thinking about it. If you’re not into mass production anymore, how can you then convert to small batch production, for instance? All the technology was designed for mass production. So people had to innovate and figure out how they could repurpose this stuff. And some of it wasn’t for audiophiles, by the way. I don’t know if you’ve ever listened to an embossed disc…
No.
These aren’t cut; the grooves are literally impressed into plastic rather than actually cutting the grooves into plastic. This had been rediscovered, by the way. From the 1950s onwards, there was a big transition to tape recording. Before that, you still had people recording audio using mobile lathes, doing field recordings with them, and there was a DIY community, but that kind of completely died out when tape machines came along. But decades later, some people rediscovered how to actually make discs using lathes that were more mobile, rather than the huge Neumann and Scully lathes, which are also very difficult to get your hands on.
So, people began looking for alternatives for making records, and found some of the stuff about embossing records back from the 1930s and 1940s, and tried to get it working again, but using new materials. Different types of plastic became available, and people started experimenting. There’s this guy, Peter King, in New Zealand. He figured out a way to do an embossing technique using tungsten steel styli to emboss polycarbonate discs. The sound quality is not that great, but there’s now a community and a demand for it. It was taken up by other people like Mike Dixon (of Michael Dixon Vinyl Art) in the US, and they kept developing it further.
Audiophiles initially hated this other innovation that happened in the 1980s, which was DMM (Direct Metal Mastering). I’ve heard many people say that it’s completely soulless and sounds awful. But it was a completely new technology at the time. They were still experimenting with it. CDs sounded horrible at the beginning as well. But from what I’ve heard, if you use DMM technology today, you can create a good-sounding record.
I have a DMM that was done by Stockfisch Records – DMM-Dubplate Vol. 1 – and it’s a metal disc, and it sounds incredible. If there’s one thing I’ve found out in being in the audio industry, it’s that you can’t make assumptions, because so much of the final result and sound quality is in the implementation, as opposed to the technology itself.
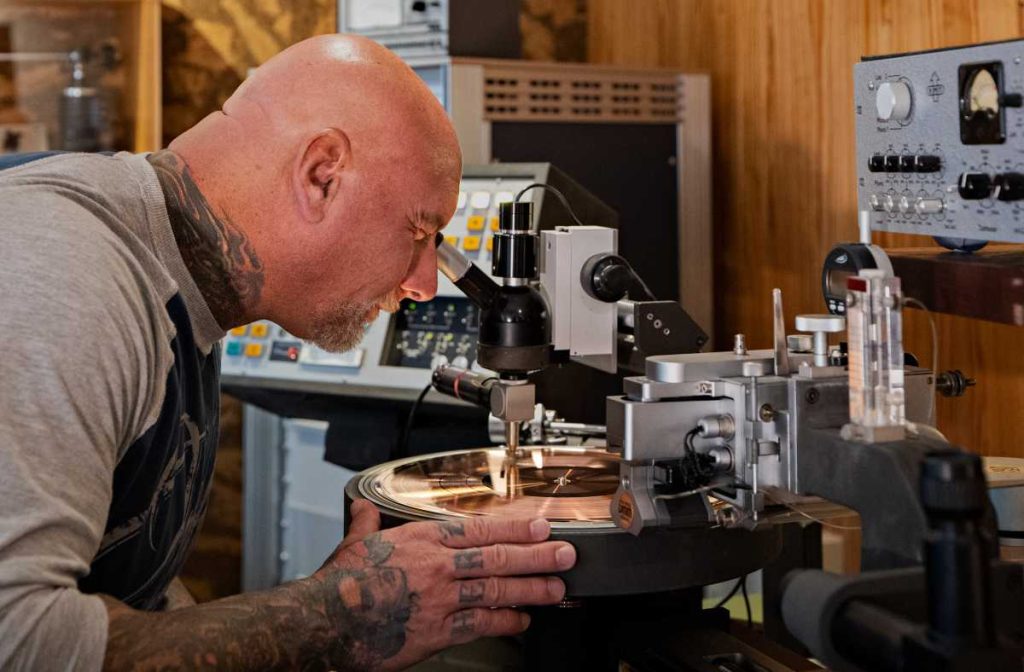
DMM wasn’t commercially successful when first introduced, but today it is. Big pressing plants are using DMM.
People often say that today, vinyl records are made exactly the same way as they were back in the 1970s. And to some extent that’s true. But there are interesting variations. People began experimenting and were doing interesting stuff, and they had the freedom to experiment because nobody cared.
And obviously, records cut from digital masters weren’t a thing until the 1980s.
And half-speed mastering isn’t exactly new. I don’t know when they came up with it, but an interesting thing I learned is that to get the most out of half-speed mastering it is actually better to use the digital source. [I’ve seen a report of half-speed mastering being used as early as 1949, and Decca implemented it in the 1950s. it became an audiophile “thing” around the mid-1970s. – Frank Doris]
You’ve stated that there is more life in declining technologies than we might expect. Another idea you’ve framed is the concept that focusing on an obsolete technology is the least risky thing a manufacturer can do, as demand can’t really drop much further, as opposed to focusing on a new technology that could really just…
Bomb. That was a quote from Steve Espanola, who runs The Secret Society of Lathe Trolls forum. He was a computer programmer, and he said that he always had to invent new programs and learn new programming languages, which became obsolete quite quickly, and he was always having to find the next thing to work on. Whereas he is now a Wurlitzer repair person, and that’s the most stable thing he could find, because there literally aren’t that many people out there who can do this work. The demand is not exactly huge, but it can’t really drop much further.
I think people may be concerned that record cutting may be a dying art, but from your research, it seems like it’s not.
I mean, you have to be careful. If everybody starts doing it, then there’s obviously going to be oversupply, and not everybody in the industry can then probably sustain that. And then it will have to become a hobby, because the commercial side of things doesn’t work if there’s too much supply compared to demand.
But the thing is, there are now opportunities out there for people to turn these things into hobbies, things that previously you would’ve said, “oh, well, you need a big company to do this.” You don’t necessarily need teams of experts today. There is a possibility to do some of this stuff that wasn’t imaginable before because of the existence of new technology. So my research is not just about moving away from new technology to just focus on the old. Sometimes it’s combining old and new technology in new ways to actually preserve the old.
For example, 3D printing is a boon in making parts that you just can’t find anymore.
There are people who use modern CNC (computer numerical control) machines, 3D printers, and things that have now become affordable even to people who aren’t working in huge multimillion dollar corporations, for instance.
When I used to be an industrial buyer, “sole source” was a phrase we never wanted to hear. Unless things have changed recently, there’s now only one source of lacquers for record mastering because of the 2020 Apollo/Transco lacquers fire that destroyed that company’s manufacturing capability.
It’s true.
That’s concerning. What happens if the remaining source has a problem?
The saving grace is that at least there is DMM, which doesn’t require lacquers for record mastering. If for whatever reason, the lacquer source completely dries up, DMM is something people could try to fall back on at least temporarily to keep it going until another provider can fill that gap. So DMM, even though it was once written off as a commercial failure, could be the savior of vinyl records.
The people at Public Records (the remaining lacquer supplier, distributed by MDC) are super-friendly, by the way. I think they get a bad rap because people think they’re this monopoly provider that is basically exploiting its monopoly, and it couldn’t be further from the truth. Their small factory is in the Nagano Valley in the Japanese Alps. It’s really a beautiful area, but not anywhere close to Tokyo or any other major city, I think. They’ve just kind of kept going. And they embody traditional Japanese values. It’s about serving. I asked the CEO, “let’s say if it’s no longer profitable to make these lacquer discs, wouldn’t you just stop doing them?” And the CEO said, “no, we would still continue to make them as long as there’s one customer, because otherwise people would be sad.” In North America, we’d be immediately completely cynical and say, well, of course that makes no sense. But that is the Japanese way of thinking about it, which I find amazing.
To some extent the entire record pressing industry is reliant on two Japanese companies. One is this lacquer disc manufacturer (Public Records), which is a really small family business. And then there’s another family business that makes the styli used for cutting records.
We’re talking about lacquer cutting. For DMM cutting, realistically there are also not more than two suppliers of the diamond styli you need for cutting DMM discs. And one of them is basically a one-man show.
Think of how many turntables and cartridges are sold, and it’s all made possible by the efforts of a few people.
It should make people nervous, right? Yes. But the good thing is, so far the record making industry has survived because people continue to come into it. There are enough passionate people that given the chance they will dedicate their lives to this.
You have mentioned that we need to change how we think about technological progress, and that it’s not just the new replacing the old; it’s about increasing options. Sometimes we think that the new replacing the old is literally the definition of progress. But you’re saying it’s more about increasing options. For example, solid-state technology didn’t push vacuum-tube technology aside for audiophiles and musicians.
It’s almost philosophical in a way. Vacuum tubes and solid-state are different. They are also to some extent interchangeable, which is, again, good in terms of resilience. If one of them should no longer exist, you at least have the other alternative. But not only that, they can serve different purposes. It’s quite myopic to think that, oh, well, progress is just clearing away the old and completely adopting the new, whereas, if we think about it, some of these old things can still generate a lot of value. And really, we lose something if we just get rid of the old. People often say to me, oh, well, that’s just nostalgia. And I don’t believe it is. It’s not a desire for the return to the old. It’s appreciating that there is value in these different things and that we shouldn’t take them for granted.
You’re an organizational sociologist. You study behaviors. Did you get turned onto this whole vinyl thing by accident, or because you’ve been an audiophile?
I think I’ve always had some kind of a resistance to the more narrow-minded view of what business and management studies are supposed to be about. For instance, that it’s always about financial profitability, whereas in the vinyl industry, it obviously is not always about financial profitability. I think that’s an important thing to recognize that even though businesses are there to be financially sound, to remain in business it’s not always the objective to make as much money as possible, and that actually, businesses can serve a greater purpose. I think that’s why I’ve been drawn to the arts and to music, because obviously you need businesses to sustain all this stuff, but it is, again, for some kind of greater purpose.
And I think you can see how emotional some people get about keeping an old technology alive. I’ve been tying this to ethics in a way, which is that I think it is inherently ethical to do something like this because it gives people joy. And the other thing is the aesthetic experience. That’s another area that I’ve become more and more involved in my research: the whole topic of organizational aesthetics. For me, it comes down to these kind of questions about ethics and aesthetics, and in business and economics, the aesthetic dimension usually just goes out the window. Nobody cares about that, which is crazy because of course, life is about aesthetics, right?
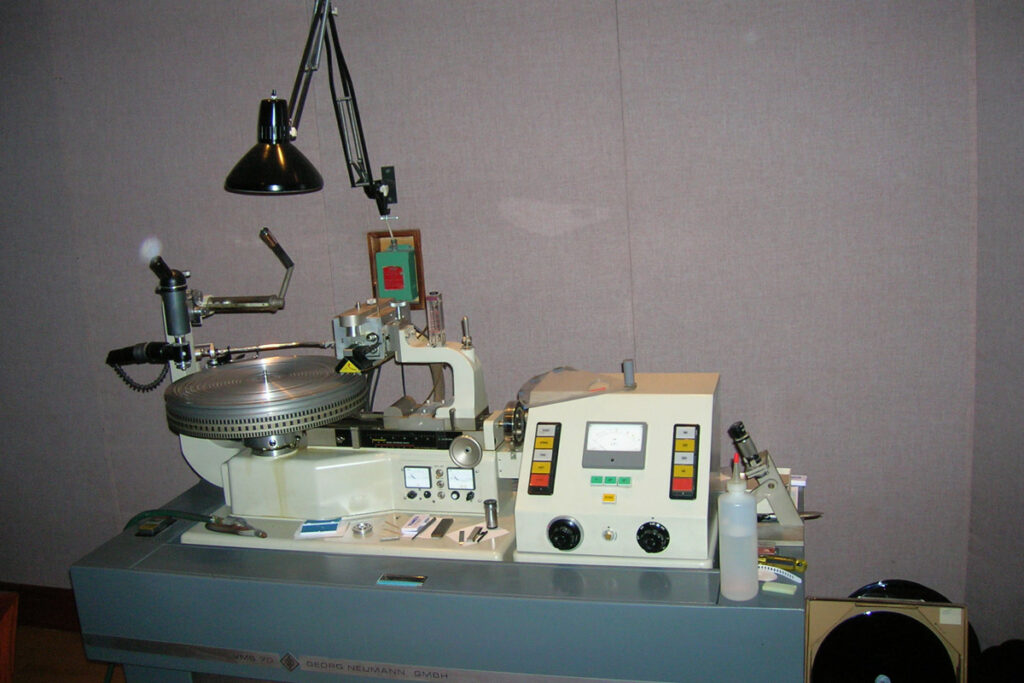
Almost everyone I know in the audio industry got into it for a love of music, but as you say, you have to be able to implement it. If you’re a musician and you want to make a sound, you have to have a guitar, which is made by a company that has to make a profit. But so many of the people who are in the audio and music industries are very passionate about it, and it’s all intertwined.
What you’re saying is pretty much why vinyl records have been kept alive. If it had just been about people thinking about profitability, all of them would’ve exited.
Have you heard of Flo Kaufmann in Switzerland?
Yes, of FLOkaSon, the disc cutting maker.
He calls the 1990s the golden age of vinyl records, whereas for most people, that’s the time of its almost quasi-death. And it was because that’s when the people who were really passionate about it suddenly had the possibility to experiment with this stuff themselves. They literally went to junkyards in the 1990s to get some of these pressing machines, and even in some cases, possibly lathes, although I’ve heard different stories about whether or not lathes were ever really thrown into junkyards. But this is when you had these people cobbling together secondhand stuff, making it work, and just making records. I’m sure most of them sounded horrible, but that was part of the learning curve, and it was because of the passion. No longer did you have to have a deal with a label or broker, and the pressing plant, and a long bureaucratic, complex process.
The concepts you talk about could apply to many things: that there is more life in declining technologies than you might think, and that diversification in technologies is good. Also, that you should think in terms of a lot of small providers to serve your needs, as opposed to one big monolith.
Based on what I’ve learned about vinyl manufacturing, I’m now looking at other settings. We talked about Japan. They’re still making katana swords, and that is also a very interesting craft that has been kept alive, and which demands extreme dedication.
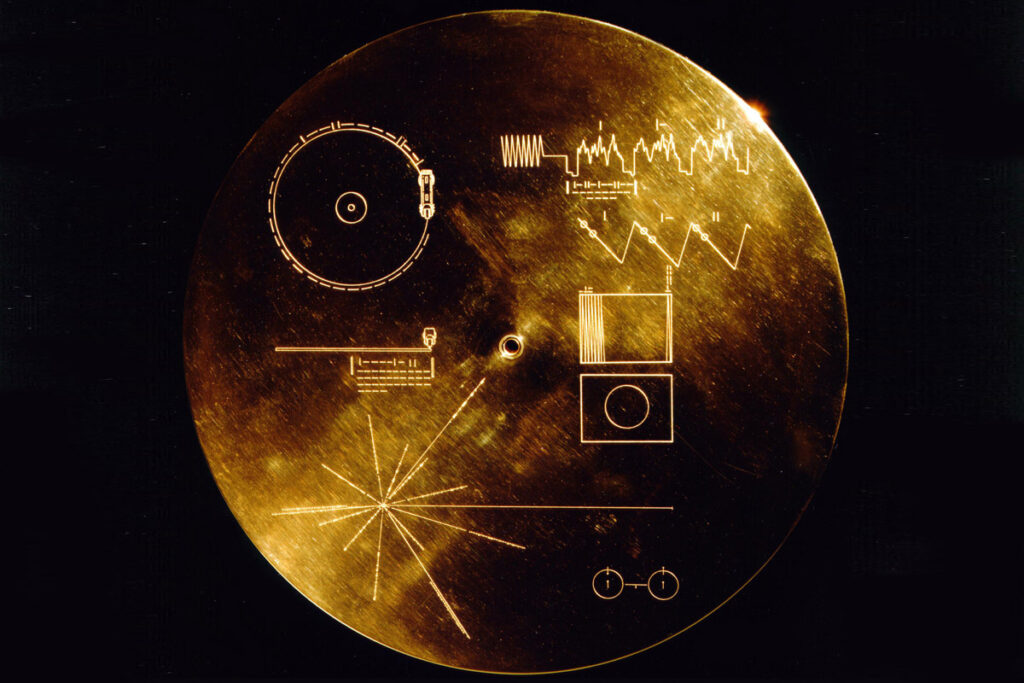
Special thanks to Copper Magazine